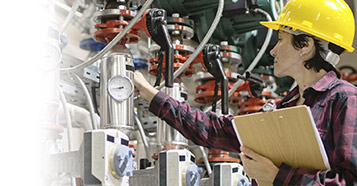
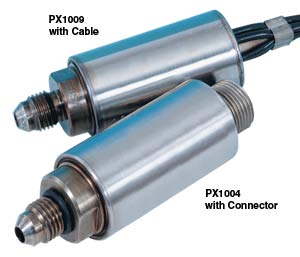
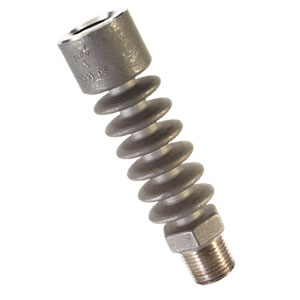
High Temperature Pressure Transducer
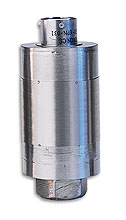
A high temperature pressure transducer doesn’t contain electronic components, giving it a much higher tolerance for heat than normal pressure transducers. These devices are typically rated for room temperature up to 343°C (649.4°F), depending on the specific model. A quality pressure transducer of this type can provide highly stable measurements at high temperatures. For example, some models can measure pressure with an accuracy of 0.25% and a thermal drift of 0.1% at 38°C (100°F).
The pressure range of a high temperature pressure transducer can vary greatly, from 15 pounds per square inch (psi) to more than 10,000 psi. A calibration record from the National Institute of Standards and Technology (NIST) may be available for these pressure transducers. Manufacturers may also calibrate their transducers at various stages in their lifecycle.
This high level of performance is possible through the use of thin film technology, which uses sputter deposits to form a molecular bond between the gauge and substrate. This manufacturing technique virtually eliminates changes to the transducer’s calibration, including creep, drift, and shift. High temperature pressure transducers should also have a pressure cavity made of stainless steel and a double-isolated case to ensure integrity of the unit in a harsh operating environment. An all-welded construction will further increase a pressure transducer’s tolerance for physical stress.
Amplification
High temperature pressure transducers provide a millivolt output, meaning that they require an external amplifier to convert it into a 4 to 20 mA or 0 to 10V signal. The need for an external amplifier will also increase the price of the system.
A new technique for transmitting temperature from a transducer to a display device involves mounting a DIN amplifier on a rail. This approach allows the amplifier to accept many common inputs and processes for temperature signals. The output may use only two wires, although a 3-wire outlook will isolate the voltage. An amplifier that uses a dual-relay output should also isolate the relays from each other. The output signal for this type of amplifier is typically between 4 and 20 mA. The temperature range on a rail-mounted temperature transmitter should also be linear with respect to temperature.
A temperature transmitter should allow easy configuration via a USB port. This feature allows the user to connect the transmitter to a PC with a standard USB cable and upload configuration data from the transmitter. The user can then use software to make the desired changes and download the new configuration back to the transmitter. The transmitter doesn’t require additional power during this process since it’s receiving the necessary power from the USB interface.
This type of transmitter should also accept isolated inputs from a push button, with trim adjustments in the same range as the output signal. An LED indicates the trim stage during this process. The trim function should be locked if it doesn’t require adjustment during configuration. The LED indicates when the signal input is out of range during normal operations.
A new technique for transmitting temperature from a transducer to a display device involves mounting a DIN amplifier on a rail. This approach allows the amplifier to accept many common inputs and processes for temperature signals. The output may use only two wires, although a 3-wire outlook will isolate the voltage. An amplifier that uses a dual-relay output should also isolate the relays from each other. The output signal for this type of amplifier is typically between 4 and 20 mA. The temperature range on a rail-mounted temperature transmitter should also be linear with respect to temperature.
A temperature transmitter should allow easy configuration via a USB port. This feature allows the user to connect the transmitter to a PC with a standard USB cable and upload configuration data from the transmitter. The user can then use software to make the desired changes and download the new configuration back to the transmitter. The transmitter doesn’t require additional power during this process since it’s receiving the necessary power from the USB interface.
This type of transmitter should also accept isolated inputs from a push button, with trim adjustments in the same range as the output signal. An LED indicates the trim stage during this process. The trim function should be locked if it doesn’t require adjustment during configuration. The LED indicates when the signal input is out of range during normal operations.
Cooling Element
Cooling elements generally rely on the principle of convective heat transfer, which is the mechanism by which heat is transferred due to the movement of fluids. In contrast, conductive heat transfer is the transfer of energy due to molecular vibrations. In addition to cooling elements, convection is also used in many other engineering practices.
A cooling element may be able to reduce media temperature, which is usually a much cheaper solution than a high temperature transducer. This approach allows the pressure to remain unchanged, assuming the media density isn’t significantly affected by temperature changes within the normal operating range. Cooling elements will typically work in both air and water, but are unsuitable for oil media such as hydraulic fluid. A high temperature transducer must be used in these applications since the viscosity of this media is highly dependent upon temperature.
A cooling element should be constructed of stainless steel to provide maximum corrosion resistance from most process media. The nickel content of this steel is typically 1.25%, with a chromium content in the range of 0.65% and 0.8%. The cooling element should tolerate a maximum pressure of 5,000 psi at 38°C (100.4°F) and 3,500 psi at 400°C (752°F). It should also reduce the temperature of a liquid process from 260 to 38°C (500 to 100.4°F) at the sensing element.
A cooling element may be able to reduce media temperature, which is usually a much cheaper solution than a high temperature transducer. This approach allows the pressure to remain unchanged, assuming the media density isn’t significantly affected by temperature changes within the normal operating range. Cooling elements will typically work in both air and water, but are unsuitable for oil media such as hydraulic fluid. A high temperature transducer must be used in these applications since the viscosity of this media is highly dependent upon temperature.
A cooling element should be constructed of stainless steel to provide maximum corrosion resistance from most process media. The nickel content of this steel is typically 1.25%, with a chromium content in the range of 0.65% and 0.8%. The cooling element should tolerate a maximum pressure of 5,000 psi at 38°C (100.4°F) and 3,500 psi at 400°C (752°F). It should also reduce the temperature of a liquid process from 260 to 38°C (500 to 100.4°F) at the sensing element.