Temperature probes
How to choose the right temperature sensor type?
Choosing a temperature sensor for your application can be an overwhelming task. The current range of sensors in the market is broader than ever, and it is easy to feel lost if you are not familiar with calibrations.
This article is here to explain the differences between the three main kinds of temperature sensor: thermocouples, RTDs and thermistors. After reading it, you will understand the pros and cons of each type and how to identify them.
With this new knowledge, you will then be able to choose the most suitable type of temperature sensor for your application.
Three types of temperature sensor
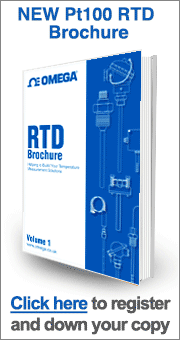
Like all technologies, temperature sensors have evolved considerably over the years. Today, three core types are used across industry.
Thermocouples
A thermocouple uses two metal wires to produce a voltage relative to the temperature present in the junction between them. There are many specialised kinds of thermocouples – they can combine different metals to measure various characteristics and temperature ranges, and produce specialised calibrations.
Read about thermocouples in more detail here.
Resistance temperature detectors (RTDs)
An RTD sensor measures temperature based on the resistance changes in a metal resistor inside. The most popular RTDs, called PT100 sensors, use platinum and have a resistance of 100 ohms at 0°C.
Read about PT100 sensors in more detail here.
Thermistors
A thermistor is like an RTD, but contains a ceramic or polymer resistor instead of metal.
Read about thermistors in more detail here
Sensor type |
Thermistor |
RTD |
Thermocouple |
Temperature Range (typical) |
-100 to 325°C |
-200 to 650°C |
200 to 1750°C |
Accuracy (typical) |
0.05 to 1.5°C |
0.1 to 1°C |
0.5 to 5°C
|
Long-term stability @ 100°C |
0.2°C/year |
0.05°C/year |
Variable |
Linearity |
Exponential |
Fairly linear |
Non-linear |
Power required |
Constant voltage or current |
Constant voltage or current |
Self-powered |
Response time |
Fast 0.12 to 10s |
Generally slow 1 to 50s |
Fast 0.10 to 10s |
Susceptibility to electrical noise |
Rarely susceptible High resistance only |
Rarely susceptible |
Susceptible / Cold junction compensation
|
Cost |
Low to moderate |
High |
Low |
Comparing thermocouples, RTDs and thermistors
The suitability of each sensor type depends on your application. It is therefore impossible to say which kind is best overall.
Key advantages and disadvantages of each sensor are summarised in the table below.
Sensor type |
Advantages |
Disadvantages |
Thermocouple |
Temperature Range Self-powered No Self-heating Rugged |
Cold-junction compensation Accuracy Stability TC extension leads |
RTD |
Accuracy Stability Linearity |
Lead resistance error Response time Vibration resistance Size |
Thermistor |
Sensitivity Accuracy Cost Rugged Hermetic Seal Surface mount |
non-linearity Self heating Narrow ranges |
Thermocouple Vs RTD
As I said above, it is not practical to compare RTDs and thermocouples generally. However, if we compare their performance in terms of specific criteria, we can see which is best suited for specific applications.
Temperature range: Thermocouples are best for working at high temperatures. New manufacturing techniques have improved the measurement range of RTD probes, but more than 90% of RTDs are designed for temperatures below 400°C. In contrast, some thermocouples can be used at up to 2500°C.
Cost: Thermocouples are generally cheaper than RTDs. An RTD will often cost two or three times more than a thermocouple with the same temperature and style.
Savings can be made on RTD installation, which is cheaper as inexpensive copper wire is used. However, this saving is not enough to compensate for the higher device price.
Sensitivity: While both sensor types respond quickly to temperature changes, thermocouples are faster. A grounded thermocouple will respond nearly three times faster than a PT100 RTD.
The fastest-possible temperature sensor is an exposed tip thermocouple. However, manufacturing improvements have also greatly improved the response times of thin-film PT100 probes.
Accuracy: RTDs are generally more accurate than thermocouples. RTDs have typically an accuracy of 0.1°C, compared to 1°C for most. However, some thermocouple models can match RTD accuracy.
The many factors that can affect sensor accuracy include linearity, repeatability or stability.
Linearity: The temperature-resistance relation in RTD is almost lineal in the sensor range, while a thermocouple has an ‘S’-type plot.
Stability: RTD probe readings stay stable and repeatable for a long time. Thermocouple readings tend to drift because of chemical changes in the sensor (such as oxidation).
RTDs’ linearity and lack of drift make them more stable in the long term.
Conclusion:
Thermocouples are more economical than RTDs due to their cheaper manufacturing process. Depending on the number of probes that you need for your application, this can be a major factor.
RTDs, on the other hand, provide a more reliable output. After carefully determining the range and the performance required, you can now select the most suitable sensor type for your application.
RTD vs Thermistor
In recent years, thermistors have become increasingly popular due to improvements in meters and controllers. Today’s meters are flexible enough to allow users to set up a broad range of thermistors, and to interchange the probes easily.
However, unlike RTDs which offer established standards, thermistors curves vary depending on the manufacturer. A thermistor’s system electronics need to match the curve of sensor.
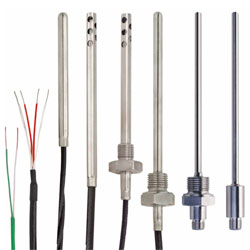
The main difference between RTDs and thermistors is the material they are made of. While RTD resistors are pure metal, thermistors are made with polymer or ceramic materials.
As in the previous section, I am going to compare specific criteria rather than comparing thermistors and RTDs in general.
Range: Unlike RTDs, thermistors can only monitor a smaller range of temperature. While some RTDs can reach 600°C, thermistors can only measure up to 130°C.
If your application involves temperatures above 130°C, your only option is the RTD probe.
Cost: Thermistors are quite inexpensive compared with RTDs. If your application temperature matches the available range, thermistors are probably the best option.
However, thermistors with extended temperature range and/or interchangeability features are often more expensive than RTDs.
Sensitivity: Both thermistors and RTD react to temperature changes with predictable changes in resistance. However, thermistors change resistance by tens of ohm per degree, compared to a smaller number of ohms for RTD sensors. With the appropriate meter, the user can therefore obtain more accurate readings.
Thermistor response times are also superior to RTDs, detecting changes in temperature much faster. The sensing area of a thermistor can be as small as a pin head, delivering quicker feedback.
Accuracy: Although the best RTDs have similar accuracies to thermistors, RTDs add resistance to the system. Using long cables can alter readings outside of acceptable error levels.
The larger the thermistor, the higher the resistance value of the sensor. If you are dealing with long distances and there is no option to add a transmitter, a thermistor is the better solution.
Conclusion:

The main difference between thermistors and RTDs is the temperature range. If your application involves temperatures above 130°C, the RTD is your only option.
Below that temperature, thermistors are often preferred when accuracy is important. RTDs, on the other hand, are chosen when tolerance (i.e. resistance) is important. In short: thermistors are better for precision measurement and RTDs for temperature compensation.
How to identify a thermocouple, RTD or thermistor probe
If you really want to know your temperature sensors, here is how to recognise each type on sight.
Thermocouple:
Thermocouples are the easiest temperature sensor to identify. A thermocouple probe has two wires identified by a colour code.
When identifying a thermocouple, it is important to determine the calibration. The most popular calibration is type K, while type T is mainly used in the USA.
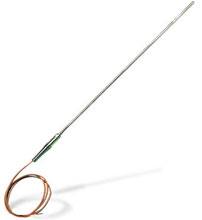
See the complete
thermocouple colour code standard.
Sometimes you will see a thermocouple probe with four wires – this is a double probe. In double probes, you will find two identical thermocouples inside the construction.
Thermistors and RTDs:
Thermistors and RTDs feature either two, three or four wires that are red and white, or red and black. The red wire is the excitation, while the black or white is the ground.
To determine whether the sensor is a thermistor or RTD, as well as the type, you must measure the resistance between the two different-coloured wires:
- An RTD PT100 will have a resistance of 100 ohms at 0 °C
- An RTD PT1000 will have a resistance of 1,000 ohms at 0 °C.
If the probe has a much higher resistance value, then it must be a thermistor. However, it will be harder to identify which type of thermistor is if you do not know the resistance-temperature curve of the element. As I explained earlier, there is no standard for thermistors; readings vary depending on the manufacturer.
Typical use cases for each sensor type
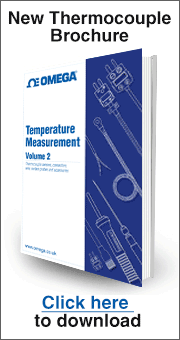
I have noted several times that temperature sensor type should be selected based on your application. Many applications can be served by more than one type of sensor.
Let us conclude, then, by summarising the value of choosing certain types in various situations.
Thermocouples
Thermocouples are the most commonly used temperature sensors in industry. There are many reasons for this.
Vibration resistant: Firstly, thermocouples are the most robust sensor type. They are simple in design, making thermocouples resistant to vibrations.
Read our white paper on this problem.
Low cost: Secondly, because thermocouples are inexpensive, they are the best option when several sensors are needed in the same application. There are certain applications that used hundreds, and even thousands, at the same time. Thermal profiling in the automotive industry is one example.
Highest temperatures: Thermocouples are the only contact sensors that can measure high temperatures. Anything that goes above 650°C requires a thermocouple probe to be measured.
Fast response: Finally, when a fast response is needed, an exposed junction thermocouple provides the fastest feedback to temperature changes.
RTDs
RTDs also offer several unique features and benefits.
High temperatures: RTDs are suitable when accuracy is required at high temperatures, as they can measure up to 650°C. This range is much higher than thermistors.
Electrical noise immunity: In addition to provide good accuracy, RTDs feature high immunity to electrical noise. PT100s are the best option for applications in industrial automation environments, where motors, generators and other high voltage equipment are around.
Less affected by environment: Lastly, if the application is in a harsh environment, an RTD element’s protective casing provides good immunity from most environmental problems; especially in comparison to thermocouples.
Thermistors
Thermistors are the best option for measurements below 150°C.
Best sensitivity: On the one hand, thermistors have the best performance on that range, even better than RTDs, specially because its best sensitivity.
Low cost: On the other hand, thermistors are 2 or 3 times cheaper than RTDs and that it is the main raison why thermistors are used in common house appliances, AC units or water heaters.
Your application
Having read this article, you should now have a much clearer idea of which type of temperature sensor is most suitable for your application.
If you still have questions, the OMEGA engineers and sales team are here to help. We can help you choose the best temperature sensor for your measuring system – contact us today.
temperature probe | Related Products